Heavy vehicle pre-start checklists are an essential part of any mining operation. These checklists help ensure that heavy vehicles are safe and ready to use before they are put into service. By performing these checks, mining companies can reduce the risk of accidents and improve the overall safety of their operations.
One of the main reasons for implementing heavy vehicle inspection is to identify and fix any problems or defects before the vehicle is used. This can include anything from checking the tires for proper inflation to examining the brakes for wear. By performing these checks, mining companies can ensure that their trucks are in good working order and reduce the risk of equipment failure or malfunction.
Another important reason for using heavy vehicle pre-start checklists is to ensure compliance with safety regulations. The mining industry is heavily regulated, and there are strict guidelines in place to ensure the safety of workers and the general public. By performing these checks, mining companies can ensure that they are in compliance with these regulations and reduce the risk of fines or other penalties.
In addition to identifying and fixing problems, heavy vehicle pre-start checklists can also help improve the efficiency of the mining operation. By performing these checks regularly, mining companies can ensure that their heavy vehicles are in top condition and ready to work at a moment's notice. This can help reduce downtime and improve productivity, which can have a positive impact on the bottom line.
What does a Heavy Vehicle Pre-start Checklist cover?
There are several steps that should be included in a heavy vehicle pre-start checklist. Some of the most important items to include are:
- Inspection of the vehicle's exterior for any damage or debris that could impact its performance.
- Checking the vehicle's tires for proper inflation and wear.
- Inspection of the brakes for wear and proper functioning.
- Checking all fluid levels, including oil, coolant, and transmission fluid.
- Examination of the vehicle's lights and signaling equipment to ensure they are working properly.
- Testing the vehicle's horn and other warning devices.
- Inspection of the vehicle's fuel system for leaks or other issues.
- Ensuring the vehicle's safety equipment, such as seat belts and fire extinguishers.
- A thorough investigation of the condition of the trailer.
It is important to note that these checklists should be customized to fit the specific needs of each mining operation. Different types of heavy vehicles may have different requirements, and it is up to the mining company to determine what checks are necessary to ensure the safety and performance of their equipment.
In conclusion, heavy vehicle pre-start checklists are an essential part of any mining operation. By performing these checks, mining companies can ensure the safety and performance of their heavy vehicles, improve efficiency, and ensure compliance with safety regulations. Implementing a thorough and effective pre-start checklist is an important step toward creating a safer and more productive mining operation, and Grid helps you achieve this at an unprecedented rate. Grid automates filing, storing, and managing all your checklist data in the fastest way possible. In fact, all you have to do is download our digital Heavy Vehicle Pre-start Checklist system with a single click, and your system is all set up within minutes!
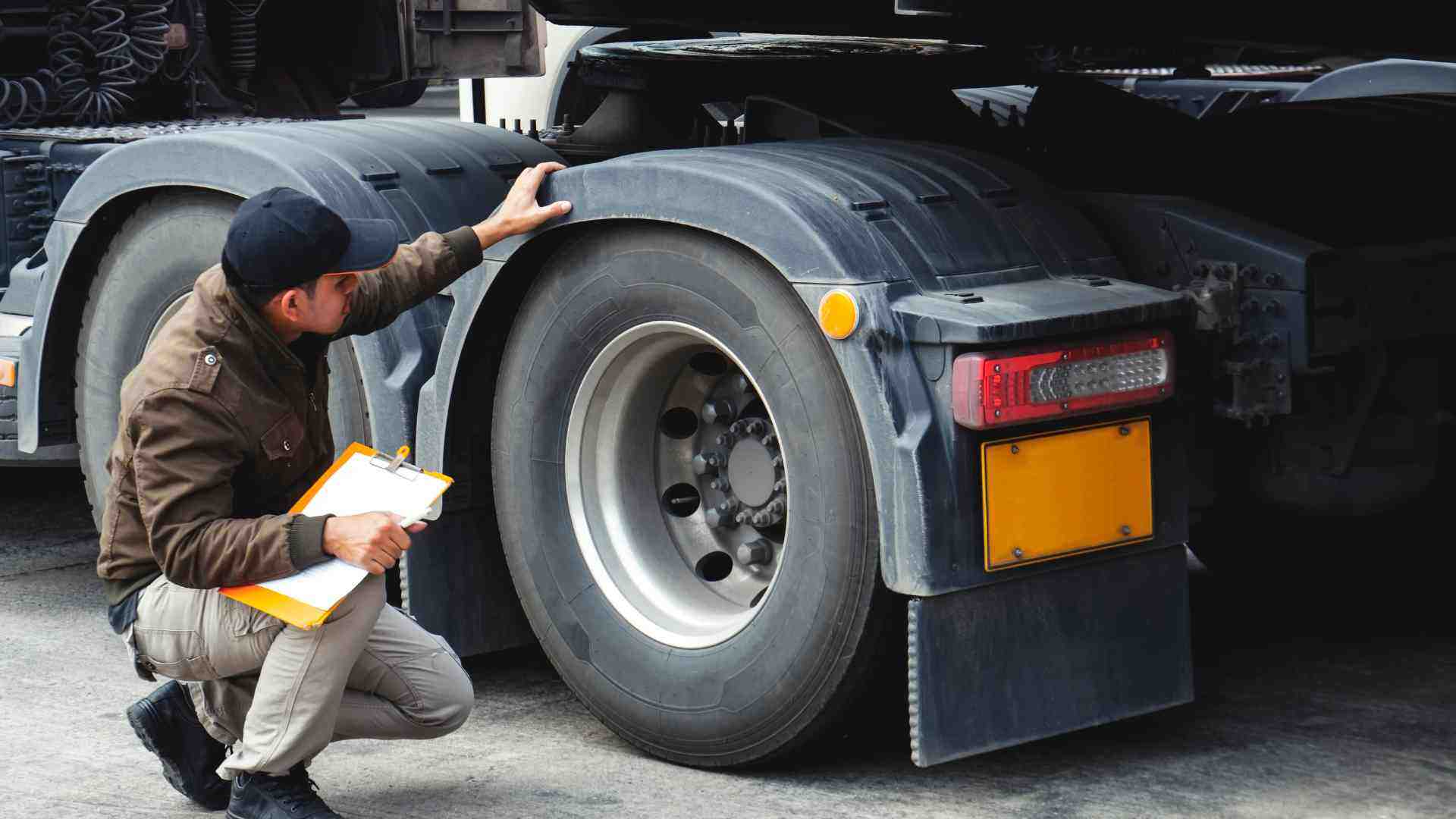
How Grid digitizes your Heavy Vehicle pre-start inspection?
Being a no-code platform that templatizes all your tasks, Grid automates filling, storing, and managing all your checklist data in the fastest way possible, on our expert-proven Checklist System. Grid factors in the following criteria:
- Location - On your mobile device, the Grid app automatically detects the geolocation of the user when the vehicle inspection is conducted.
- Asset ID - Every asset has an ID that's stored in the Masters workspace on the Grid app, which can then be entered along with the Registration Number to identify and track every vehicle.
- Windscreen - Operating in rough terrains means windscreens are susceptible to the accumulation of dirt or cracks, both of which should be inspected to rule out visibility issues.
- Brakes - Drivers need to check if the brakes and handbrakes are not just operational but in perfect working condition.
- Dashboard - Dashboards are essential as they update drivers with necessary vehicle warnings and readings. Every panel must be checked after turning on the ignition.
- Steering Wheel - Steering wheels must be tested before every trip because any form of loss of control can lead to injuries or even fatalities.
- Recovery Kit - No trip should be initiated without the presence of the complete recovery kit. Users need to enter all the components present in the toolkit, like wheel jack, jumper leads, toolkit, tire repair kit, etc.
- Radio - Mine sites occupy a massive area, which means vehicles may be far apart from the nearest point of contact. This means that all radio communication needs to be working to-and-fro, for quick response.
- Tires - Drivers must be on top of their tire condition, as any faults here combined with the demanding terrain can lead to serious accidents. The form provides you the option to record the health, pressure, and presence of a spare tire.
- Lights - It's impossible to light up the whole tenement, and at multiple times and areas, drivers might face low visibility conditions. This is when drivers must ensure front and rear lights are working properly.
- Tray Latch - Unlike ATVs, light vehicles like pickup trucks are loaded with equipment, hence to avoid losing any material, ensure that the tray latch is operational.
- Fluids - Grid users need to check for any form of leak, and also if the coolant, engine oil, washer fluid, and fuel are in an adequate amount along with reserves.
- Battery - The batteries must be regularly tested, along with the examination of the water level indicator.
- Cables - All the necessary cables must be investigated thoroughly to cancel out the chances of an electrical fault when the drivers try to use a function.
- Comments - There's also the option for users to add comments or remarks to further elaborate on any issue during the inspection.
With added options to generate highly insightful dashboards, reports, and much more, this is just scraping the surface of Grid's abilities to forever transform your vehicle inspection process and productivity. Learn more about the scale at which your mining operations can grow with the edge Grid brings to your frontline processes. Don't wait, take the first step toward a safer and more efficient workspace!