Manufacturers must ensure that their quality is excellent, as producing high-quality products increases customer satisfaction, leading to repeat business and a positive reputation. High-quality product helps businesses avoid compliance violations, product liability concerns, lawsuit risks, and legal costs, as many industries have strict product quality regulations. Additionally, it distinguishes a manufacturer from its competitors, improving competitiveness and market position, especially in today's age of readily available information and alternatives. A stringent quality control process is thus essential for manufacturing companies to quickly identify and correct areas for improvement, resulting in increasingly better quality. With a robust Quality Assurance and Control (QA/QC) system, manufacturers can create state-of-the-art products, reducing resource wastage and saving costs. So how does an end-to-end QA/QC system work, and what criteria does it cover?
An end-to-end QA/QC system is a combination of step-wise processes consisting of multiple rounds of rigorous monitoring and inspection. Since the combination can vary given the unique manufacturing objectives and requirements, we'll look at the fundamental stages and the sheer impact they can have if executed consistently in real-time. The fundamental steps can be distinguished as:
- Production Readiness Assessment
- Assembly Line Production Tracking
- Post Assembly Quality Control
- Logistics Management System
How do Production Readiness Assessment Checklists work?
Production Readiness Assessment (PRA) is a systematic process used to evaluate the readiness of a manufacturing plant to begin producing goods at full capacity. It requires forms and checklists to be filled at regular intervals to ascertain readiness. The PRA process typically includes the following steps:
- Defining objectives: PRA objectives should be defined and communicated to all relevant stakeholders. These objectives include critical aspects like assembly line readiness, equipment dependability, production process accuracy, and employee training.
- Developing a plan: A plan should be developed to carry out the PRA process, including the scope of the assessment, the methodology to be used, the resources required, and the timeline.
- Conducting production assessments: These assessments should be conducted to evaluate the critical areas identified in Step 1. This includes physical inspections of equipment, process simulations, and personnel reviews.
- Collecting data: To assess the plant's overall readiness for production, data should be continuously gathered, analyzed, and compared against the defined objectives and criteria.
- Report findings: The results of the PRA process should be documented in a report. This report should contain a thorough evaluation of each critical area and a conclusion regarding the plant's overall production readiness.
- Implementing improvements: Based on the findings of the PRA reports, improvements should be identified and implemented to ensure that the manufacturing plant remains in an ideal condition.
- Monitor and refine: The PRA process needs to be monitored and improved over time in order to adapt to changing operational demands.
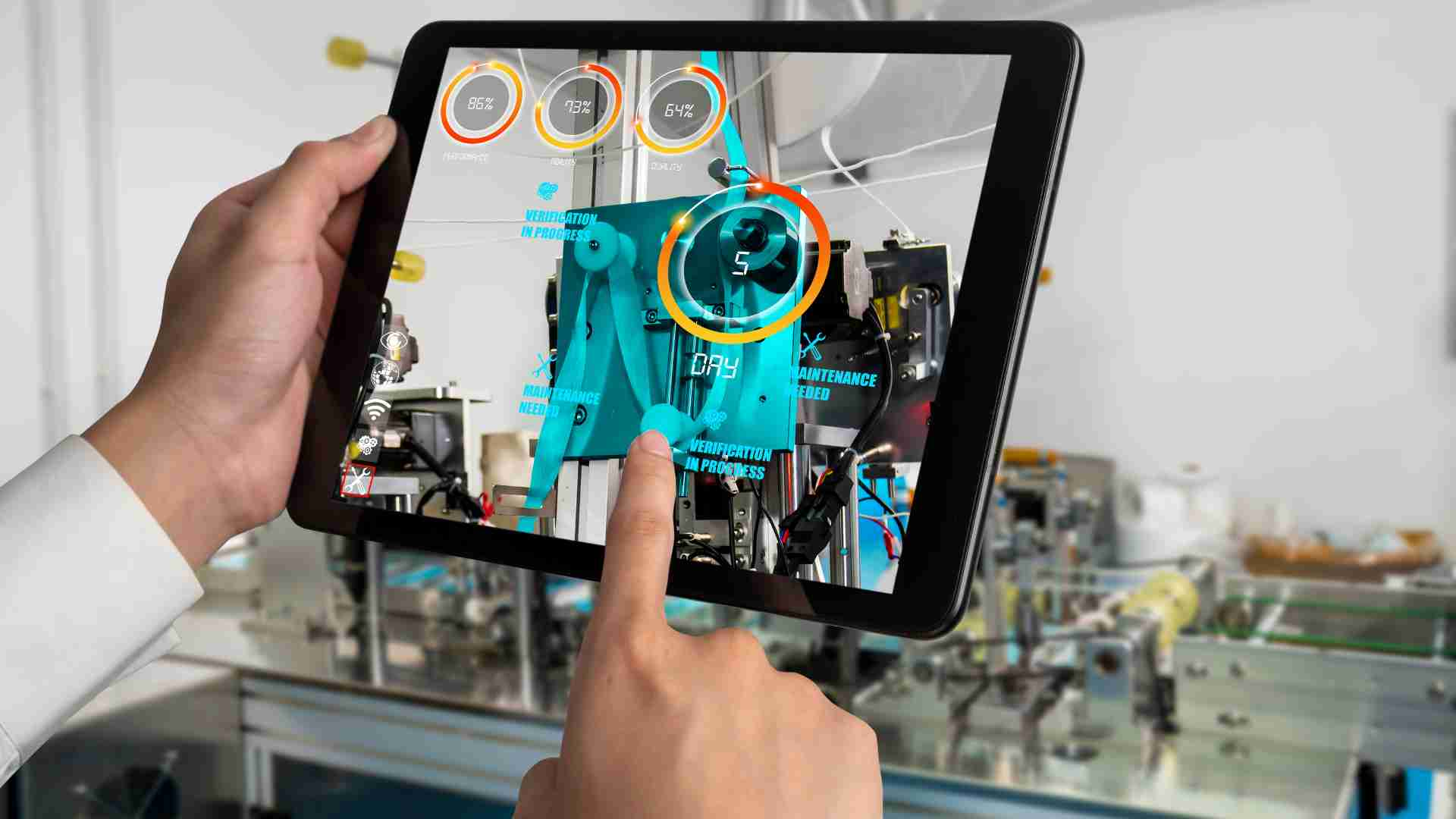
Why should you track production on an Assembly Line?
Manufacturers need a Production Tracker along their assembly lines to improve manufacturing efficiency and accuracy and to ensure that the final product meets the required quality standards. Some reasons why production tracking software is important:
- Real-time Visibility: Monitoring production provides you with real-time visibility into the key link in your value chain, enabling manufacturers to record the status of each unit as it moves down the production line. This helps identify bottlenecks, resolve issues, and enhance the production process. Visibility leads to higher traceability for every asset, allowing workers to ensure every component is assembled accurately to create the perfect product.
- Quality Control: With data being digitally recorded at the frontline, manufacturers can track and monitor each component to guarantee they meet the required quality standards and have a low risk of defects or issues. This feature saves organizations a lot of money and raw materials as it's wasteful to discover your product is faulty when it is finally ready to be packed and delivered.
- Improved Collaboration: Assembly line tracking also empowers different teams within a manufacturing facility to freely collaborate and share information, improving overall production efficiency and effectiveness.
- Equipment Performance and Maintenance: To produce high-quality products it's essential to maintain equipment quality, as equipment failures are a major reason for batch failures. Tracking can provide real-time information on equipment's performance, enabling manufacturers to monitor their health, track maintenance requirements, and preemptively plan for maintenance or upgrades.
- Workforce Utilization: Along with equipment data, manufacturers can also benefit from insights into the utilization of labor resources, helping them optimize staffing levels and improve workforce productivity.
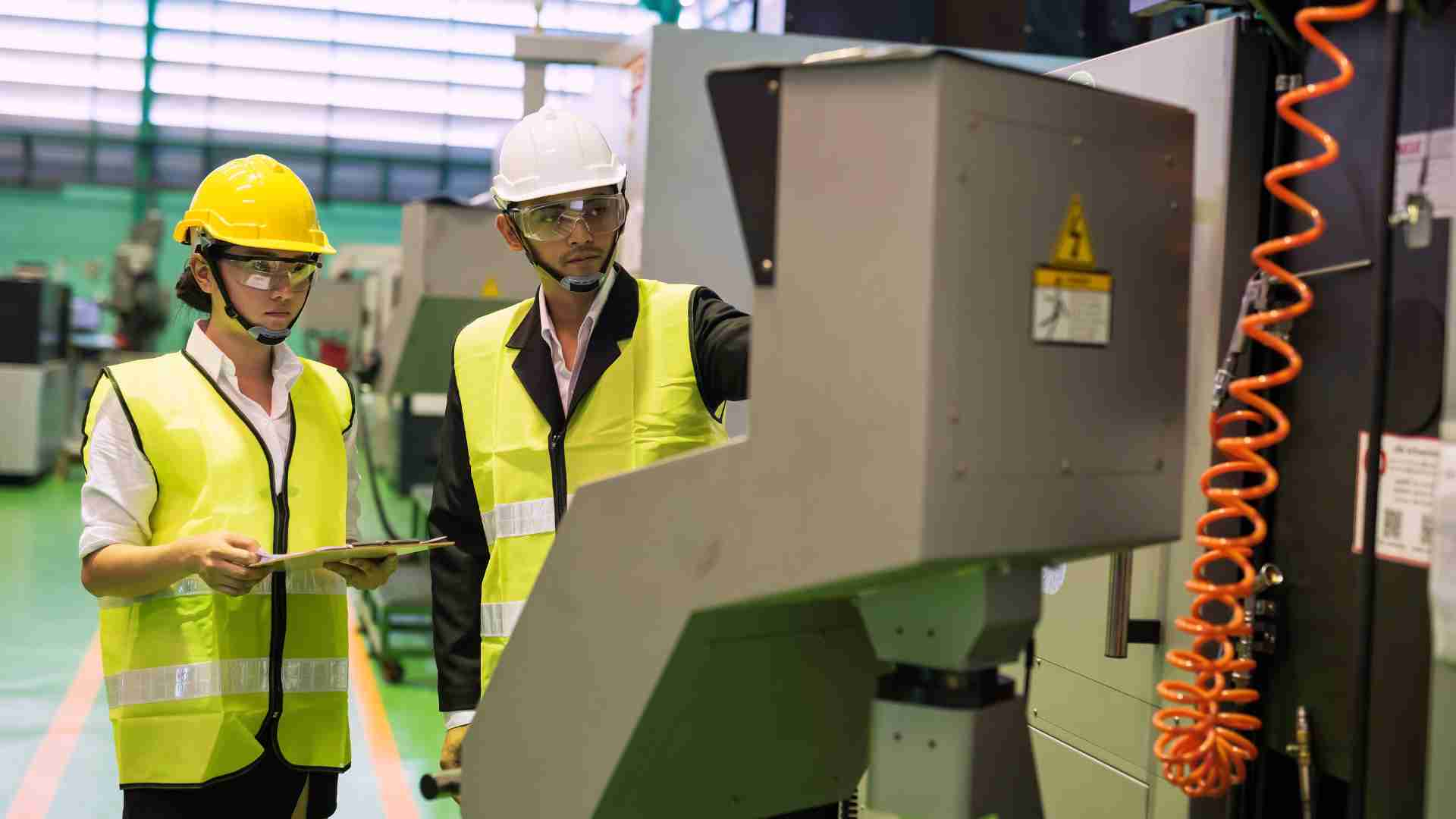
What is a Post Assembly Quality Control Checklist?
Post Assembly Quality Control Checklist is a set of procedures and checks performed on a product after it has been assembled to ensure that it meets the specified quality standards and requirements. This checklist typically includes items such as inspections for proper assembly, functional testing, measurements of key components, and checks for any defects or non-conformances. The purpose of this checklist is to catch and correct any issues before the product is released to the customer, thus maintaining the overall quality of the finished product.
The criteria in a Post Assembly Quality Control Checklist may vary depending on the type of product being manufactured and the specific requirements of the customer or industry standards. However, some common items that may be included in this checklist are:
- Physical Inspections: This includes visual inspections of the product for precise assembly and any obvious defects or damage. For example, inspecting an assembled bike to ensure the handlebars or wheels are robust, and there is no visible damage to the body.
- Functionality Testing: This involves testing the product's functionalities to check that they work as intended. Going back to the bike, this could mean checking whether the maximum speed and acceleration are as per specification or that the noise decibel levels are acceptable.
- Measurements and Tolerance Checks: Every product has a set range of dimensions that its key components should strictly conform to. A circuit board undergoes tolerance checks to verify the size and position of all the components on it, down to the millimeter.
- Electrical Testing: For products with electrical components, electrical testing is done to test and inspect before they're energized. It helps technicians filter out the chances of a short circuit or power discontinuity and even wiring issues.
- Compliance with Regulations: Every test case is written with industry standards and regulations in mind, as any deviations could lead to serious problems for the customer and the company. The impact a product can have on users' lives is taken into account when evaluating a product's quality, but the fundamental question is whether the product is secure and qualified to reach the customer in the first place.
- Documentation Review: Manufacturers must go above and beyond to review all test reports, inspection records, and certifications in order to ensure their validity and accuracy if they want to produce products of the highest quality.
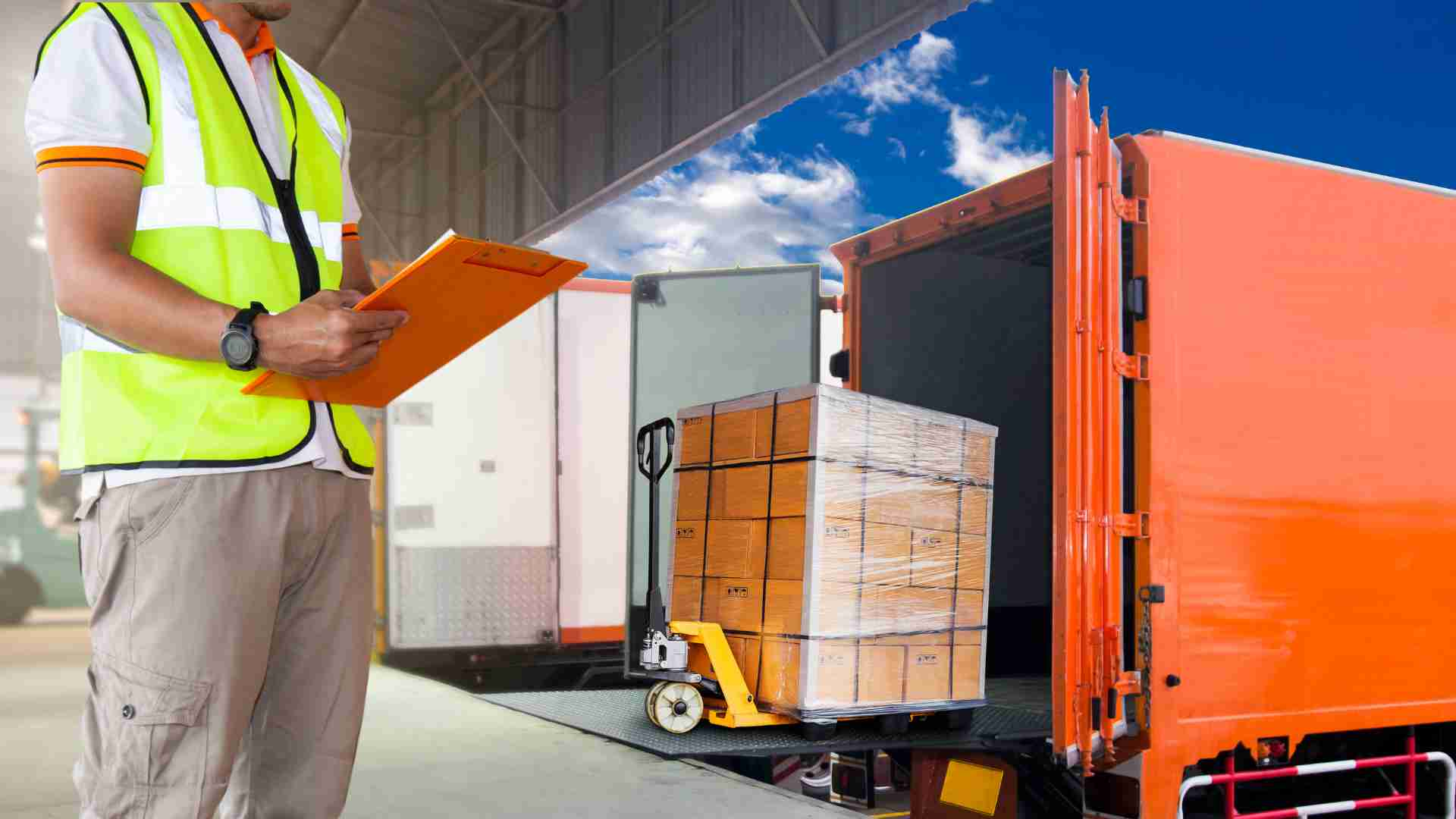
Impact of a strong Logistics Management System
A strong Logistics Management System can help improve product quality by ensuring that the right products are delivered to the right place, at the right time, and in the right condition. Here are a few ways that a strong logistics system can help improve product quality:
- Improved inventory management: A strong logistics system helps track inventory levels, allowing for just-in-time delivery of raw materials, reducing the risk of obsolescence, and minimizing the potential for defects caused by outdated or sub-standard components.
- Enhanced control over supply chain: A study by Accenture found that companies with an integrated supply chain were able to reduce their defect rate by 25% compared to companies with a fragmented one. Thus, efficient distribution increases visibility and control over the entire supply chain, allowing for quick resolution of issues that may impact product quality. By improving the overall efficiency of the supply chain, lead times and cost of goods sold are reduced, allowing companies to re-invest savings in quality control and improvement.
- Improved transportation and storage conditions: Manufacturing businesses must aim for their products to be transported and stored in conditions that meet the ideal standards for temperature, humidity, and other environmental factors that can affect product quality. Logistics leader DHL found that companies with effective temperature-controlled logistics systems had a significantly lower rate of product spoilage. As a result, products face minimal risk of damage and loss, preserving product quality and reducing the need for costly repairs or replacements.
How can manufacturers digitize their Quality Control process?
Before we address the 'how', let's address why manufacturers ought to digitize such a crucial step as Quality Control, given that many companies still favor manual procedures. First and foremost, digitization helps businesses get faster and leaner, and this has gotten critically important in a post-COVID environment. Every business should benefit from streamlined processes, improved accuracy, real-time data analysis, hassle-free data management, end-to-end traceability, and increased profitability, all of which are possible with digital transformation. Now, despite the advanced nature of software, integrating them to automate your processes is only pretty easy to accomplish, especially with technologies like No-code SaaS. No-code has been democratizing technology to ensure any type of business can adopt digitization to automate their workflows. This means manufacturers can set up and streamline their entire QA/QC process without the need for time-consuming coding. Here are a few ways that no-code technology can help improve the quality control process for manufacturers:
- Automated workflows: No-code platforms like Grid allow manufacturers to automate workflows, from inspection and testing to data analysis. This significantly reduces manual efforts and eliminates the risk of human error, leading to drastic improvements in efficiency.
- Customizable Quality Control dashboards: The best thing about no-code is that manufacturers can create completely customizable dashboards for end-to-end visibility into their operations. These dashboards can be tailored to your needs, making it easier to monitor and track key metrics, such as defect rates and production output.
- Easy data analysis and reporting: No-code technology provides manufacturers with easy-to-use data analysis and reporting tools that can help them quickly identify trends and patterns in their quality control data. With cloud-based data solutions, manufacturers can make data-driven business decisions in real-time to resolve any quality control issues.
- Integration with other systems: No-code technology can be easily integrated with a manufacturer's existing systems, such as ERP, CRM, and IoT, allowing for seamless data flow and improved efficiency.
- Lower costs and faster implementation: Compared to traditional software development, no-code technology typically requires lower costs and can be implemented faster, since there is no need for coding. Being cloud-based, no-code allows manufacturers to access digital quality control tools and systems without the need for complex and expensive IT infrastructure. This makes it an accessible and cost-effective option. In addition to this, no-code SaaS platforms are subscription based. For example, Grid users only need to pay for the services they use in contrast to the high costs and complexity associated with traditional software solutions.
Now that you know the importance of a fully digitized Quality Assurance and Control System, and how easy it is to set it up on a No-code SaaS platform, it's time to get the best results out of your operations. If you’d like to know more about how Grid can help you integrate a QA/QC system into your day-to-day operations, speak to a Grid expert and we’ll get you started.