A cost management system is a set of tools and processes used to optimize spending. By implementing a cost management system, operations managers at mineral exploration companies can improve efficiency, reduce costs, and improve overall performance.
This is incredibly important because being cost-conscious and efficient allows exploration companies to increase the chances of a valuable mineral find materializing, by allowing them to conduct more operations on a lower budget.
Overall, though, there are several key benefits to implementing a cost management system for the mineral exploration industry as a whole:
Benefits Of Cost Management Systems For Mineral Exploration Companies:
- Improved cost control: By tracking and monitoring costs on an ongoing basis, operations managers can identify areas where costs are exceeding budget and take corrective action to bring costs back in line. Usually, budget overruns are only recognized after the completion of a project or after the completion of a project's phase, because in order to measure costs in real-time, it is necessary to record and analyze operational data in real-time as well, which is not a standard practice.
- Increased profitability: Naturally, by reducing costs and improving efficiency, a cost management system can help to increase profitability for the organization. By identifying and eliminating waste, streamlining processes, and negotiating better rates with suppliers, operations managers can reduce costs and increase the bottom line.
- Enhanced decision-making: A cost management system provides operations managers with the data and insights needed to make informed decisions about the organization's costs. By tracking key performance indicators (KPIs) and other metrics, operations managers can better understand the drivers of costs and make informed decisions about how to optimize spending.
- Greater transparency: A cost management system helps to increase transparency around the organization's costs, making it easier for operations managers to see where money is being spent and identify opportunities for cost savings.
- Continuous improvement: A cost management system is an ongoing process of continuous improvement. By regularly reviewing and updating processes and procedures, operations managers can identify opportunities for further cost savings and continually improve the efficiency of the organization.
What Should The Ideal Cost Management System Track?
To optimize spending in the mineral exploration industry, operations managers should track a variety of cost heads to get a complete picture of the organization's costs. Some specific cost heads that might be relevant in the mineral exploration industry include:
- Exploration costs: The cost of exploration activities, including drilling, sampling, and geophysical surveys, can be a significant driver of costs in the mineral exploration industry. Operations managers should track exploration costs to identify opportunities for cost savings.
- Laboratory costs: The cost of laboratory testing and analysis, including assaying and metallurgical testing, can also be a significant driver of costs in the mineral exploration industry. Operations managers should track laboratory costs to ensure that they are in line with the budget and identify opportunities for cost savings.
- Personnel costs: Personnel costs, including wages, benefits, and training, can also be a significant driver of costs in the mineral exploration industry. Operations managers should track personnel costs to ensure that they are in line with the budget and identify opportunities for cost savings.
- Equipment costs: The cost of equipment, including maintenance, repairs, and replacements, can also be a significant driver of costs in the mineral exploration industry. Operations managers should track equipment costs to ensure that they are in line with the budget and identify opportunities for cost savings.
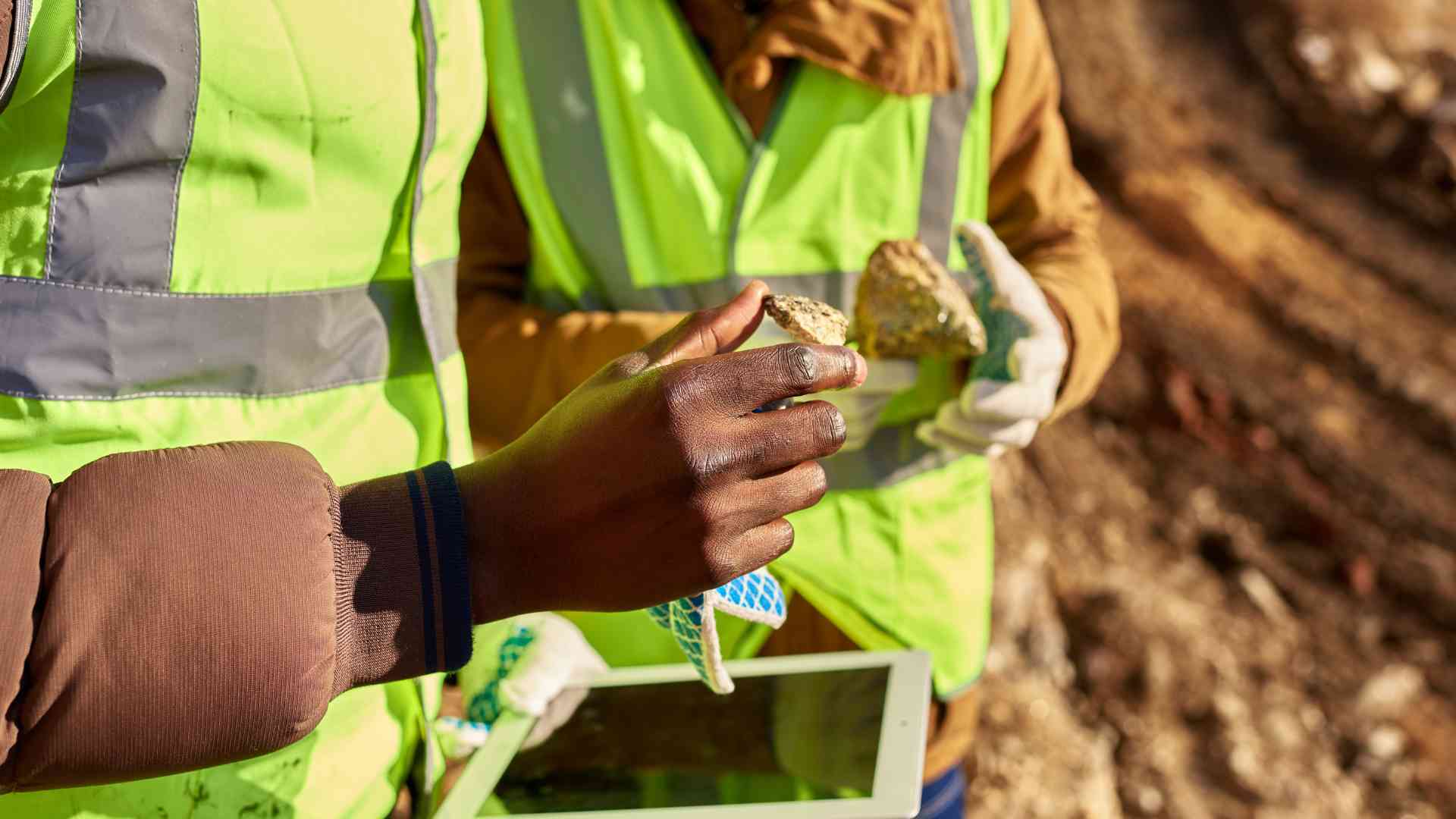
What Are Some Important KPIs that Cost Management Systems Should Track?
To ensure that they are as efficient as possible, mineral exploration companies should track a variety of KPIs and other metrics to measure the effectiveness of their cost management systems. Some specific KPIs and metrics that might be relevant in the mineral exploration industry include:
- Cost per meter drilled: This KPI measures the cost of drilling a meter of core or reverse circulation. By tracking this KPI, operations managers can identify opportunities to reduce costs and increase efficiency. See how VR Resources, a junior exploration company in Vancouver, implemented a cost-per-meter-drilled metric, using Grid.
- Return on investment (ROI): This KPI measures the profitability of an investment or project. By tracking the ROI of different cost centers or projects, operations managers can identify areas where cost management efforts are paying off and where further improvements are needed.
- Cost of quality: This KPI measures the cost of defects or errors in the exploration process. By tracking the cost of quality, operations managers can identify areas where improvements in quality can lead to cost savings.
- Inventory turnover: This KPI measures the speed at which inventory is sold and replaced. By tracking inventory turnover, operations managers can identify opportunities to reduce waste and improve efficiency.
.jpeg)
Strategic Benefits Of Implementing A Cost Management System:
By tracking these and other KPIs and metrics, mineral exploration operations managers can better understand the drivers of costs in their organization and identify opportunities for cost savings. In addition to tracking these metrics, operations managers can also implement a range of strategies to optimize spending in the mineral exploration industry, including:
- Negotiating better rates with suppliers: By negotiating better rates with suppliers, operations managers can reduce the cost of supplies such as drilling equipment and laboratory supplies.
- Implementing lean principles: By implementing lean principles such as waste reduction and continuous improvement, operations managers can reduce costs and improve efficiency.
- Streamlining processes: By streamlining processes, operations managers can reduce waste and improve efficiency, leading to cost savings.
- Implementing cost-saving technologies: By investing in cost-saving technologies, operations managers can reduce costs and improve efficiency.
- Training and development: By investing in training and development programs for employees, operations managers can improve productivity and reduce costs.
By implementing a cost management system and implementing these and other strategies, operations managers in the mineral exploration industry can optimize spending, improve efficiency, reduce costs, and increase profitability.
However, one key requirement in order to set up a cost management system is the ability to track (ideally in real-time) the various activities that comprise all the operations of the company. The closer you get to real-time information, the quicker you can respond to budget overruns, reduce superfluous costs and make the cost management process more efficient.
The bottleneck is in the gathering of the operational data, and that's where a platform like Grid comes in. Unlike traditional data-gathering methods, Grid allows you to set up simple forms and worksheets that can be filled in on-site using a regular mobile phone (even in areas with low / no network access) and then displays that information on customizable dashboards in real time. You can program in all your cost-related metrics and Grid displays the KPIs for you to track and optimize.
If you'd like to see how Grid can optimize your mineral exploration company's costs, you can book a demo, or speak to a Grid expert.