The goal of every manufacturing enterprise is to scale their business, in terms of production capacity, quality and quantity of end product, workforce, and most importantly net revenue. But attaining these results involves reworking and rebuilding hundreds of everyday processes, as lack of digitization there has created a system of recurring redundancies, irregularities, and faults.
In accordance with the Total Productive Maintenance (TPM) methodology, that focuses on blurring the distinction between production and maintenance, our no-code platform Grid empowers the entire workforce to proactively and easily maintain the factory line. Grid aggregates every personnel along the hierarchy and their respective workflow and responsibilities, and aligns them to create a single source of truth, that provides invaluable transparency and insights to decision-makers. This also ensures standardization in data collection, workplace practices, equipment monitoring procedures, workforce efficiency, and all the different stages in production.
In order to further illustrate how essential Grid can be in digitizing your production, we'll guide you through some critical losses that enterprises face on a regular basis. We'll then explain how Grid solves the root problems, and converts the losses into avenues for profit.
Performance Loss
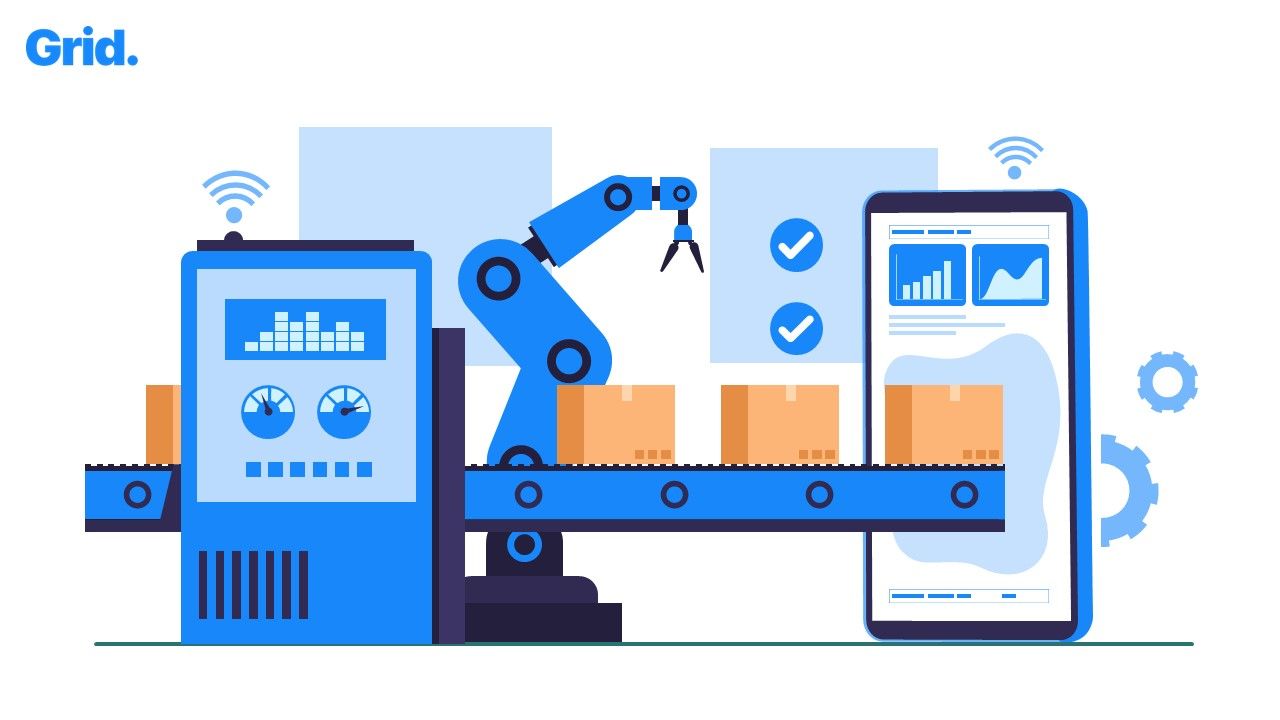
Performance in manufacturing is the comparison between the actual throughput vs the ideal throughput. Performance losses arise out of machines or processes not functioning at their maximum speed. The reasons generally range from the occurrence of micro stops to slow production cycles and are often hidden unless monitored closely, hence the need for a round-the-clock digital tracking mechanism. Performance losses are not instantaneously significant, but they are perennial, and keep adding to loss in productivity in the background.
With rigorous data collection that is possible via Grid's mobile application, and real-time analysis on user-friendly dashboards, managers and admins can determine ideal cycle times and production rates. This can then be compared with the actual cycle time, and then conduct a Root Cause Analysis to identify the issues at hand.
Production Time Loss
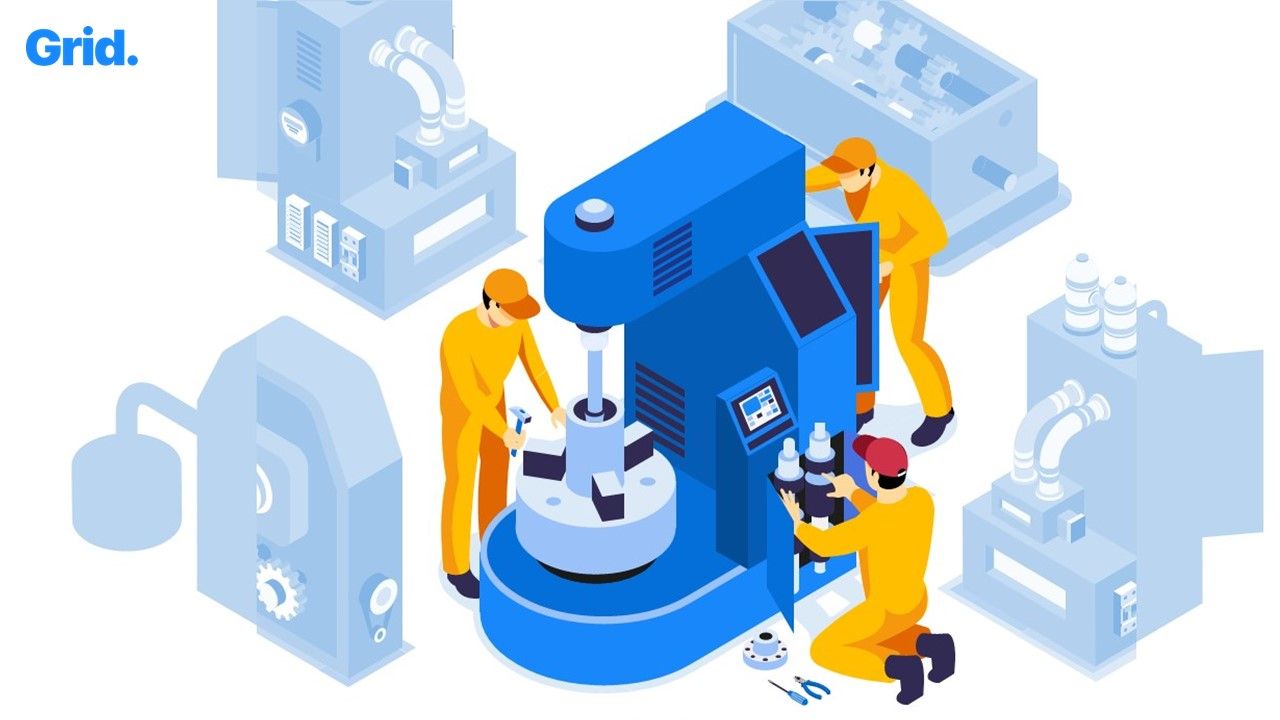
Most manufacturing businesses decline due to losses in production time that are a result of completely avoidable factors. One of them is equipment failure or unscheduled maintenance, which is a nightmare for every business, as this usually leads to a significant amount of downtime. Production standards can be adversely affected by downtime in manufacturing. In fact, according to some estimates, almost every factory loses 5% to 20% of productivity due to downtime. The annual cost of downtime to a manufacturer can be as high as 800 hours, which can lead to hundreds of thousands of dollars in lost revenue, depending on the scale of operations.
Thanks to digitization, equipment failures can be avoided or managed with accurate tracking and reporting. With Grid handling your production line, performance metrics of every machine are reported to admins who can then quickly identify irregularities that can be a sign of impending machine failure. Also, with the stats of every failure recorded in Grid's centralized database, floor managers can plan response time, maintenance personnel, and backups accordingly.
Quality Loss
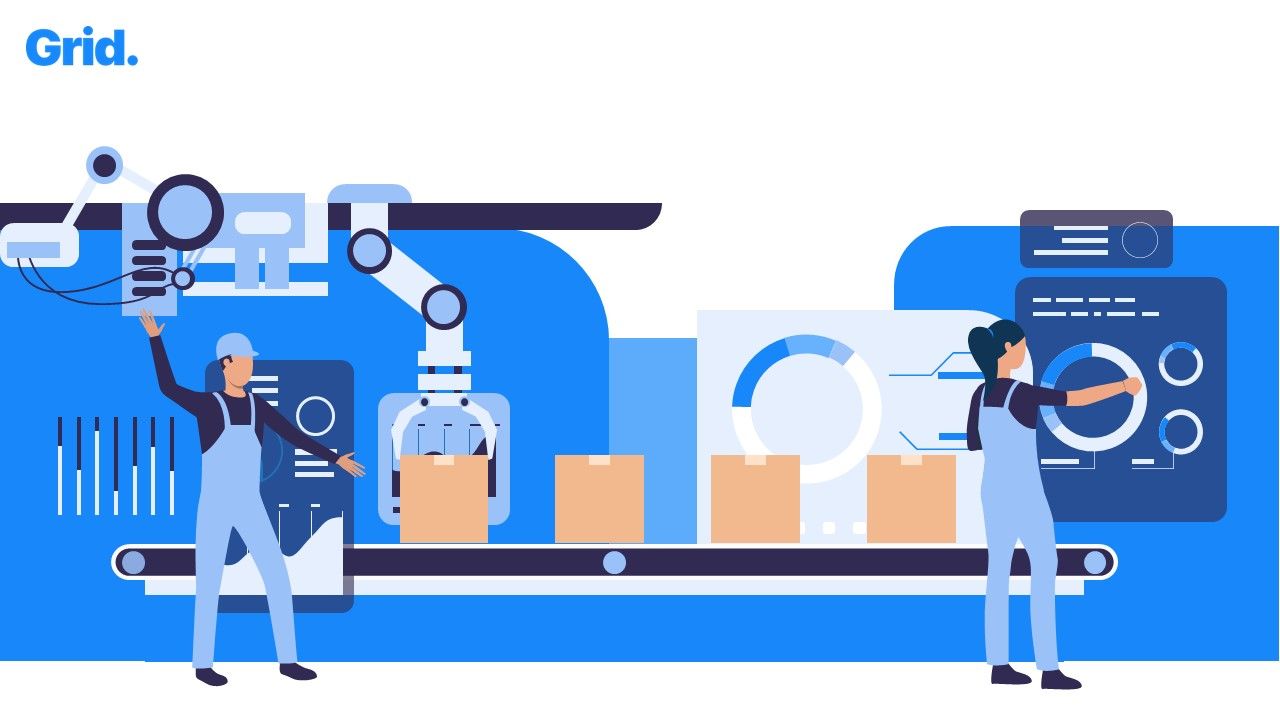
While quantity and time are definitely critical factors to gauge your process, they serve no purpose if the quality of the end product doesn't meet the desired standards. This means a waste of time, inventory, and resources, and is unfortunately an irreversible process. In many cases, a whole batch of products goes to waste, which can be a major setback depending on the product. Quality losses can be a result of machine start-up issues or steady-state production issues. Machines can produce faults due to a lack of warm-up time after start-up or incorrect settings during product changeover.
Grid enables businesses to achieve standardization in this case as well as identification of the machine and personnel that are most responsible for quality losses. managers can then take steps such as preventative maintenance, increased training, or re-assignment of personnel, to correct these issues. Managers can also build applications dedicated to identifying steady-state losses, and deep-dive into analyzing the cause.
Asset Management Loss
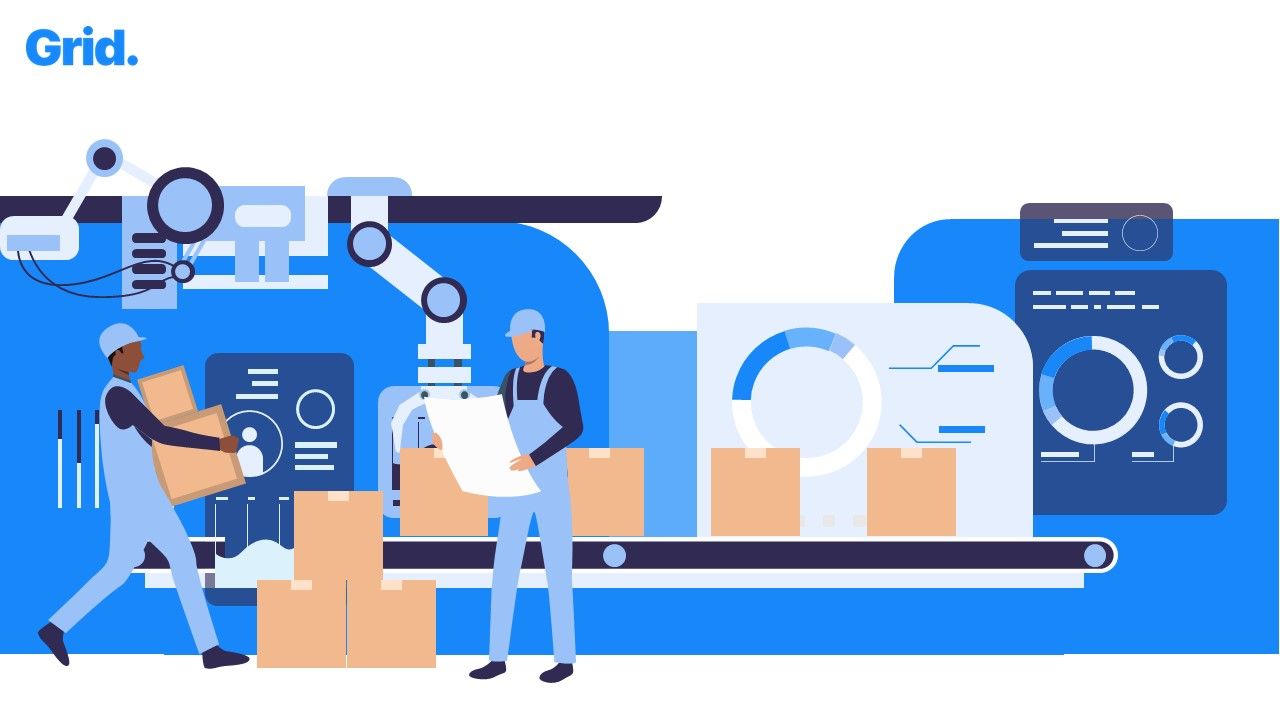
Another issue that plagues manufacturing companies is the management of assets and inventory, especially on large-scale factory lines, where inventory exceeds thousands of units a day. To ensure total synchronization of stock procurement and demand, optimal utilization of storage facilities, timely monitoring of all inventory and components, and quality checking of inventory, Grid is the all-in-one solution.
With end-to-end digitization, Grid transforms the supply chain into an intelligent network of processes. The following are just some important features in Grid that are being used in 30+ factories to revamp their asset management model:
- Automated alarms/notifications for low stock levels and supply chain anomalies
- Real-time reports of management efficiency
- Deadstock analysis
- Real-time tracking of the delivery chain using QR-code functionality
- Error-free storage cost calculations
- 100% process transparency for decision-makers
Productivity Loss
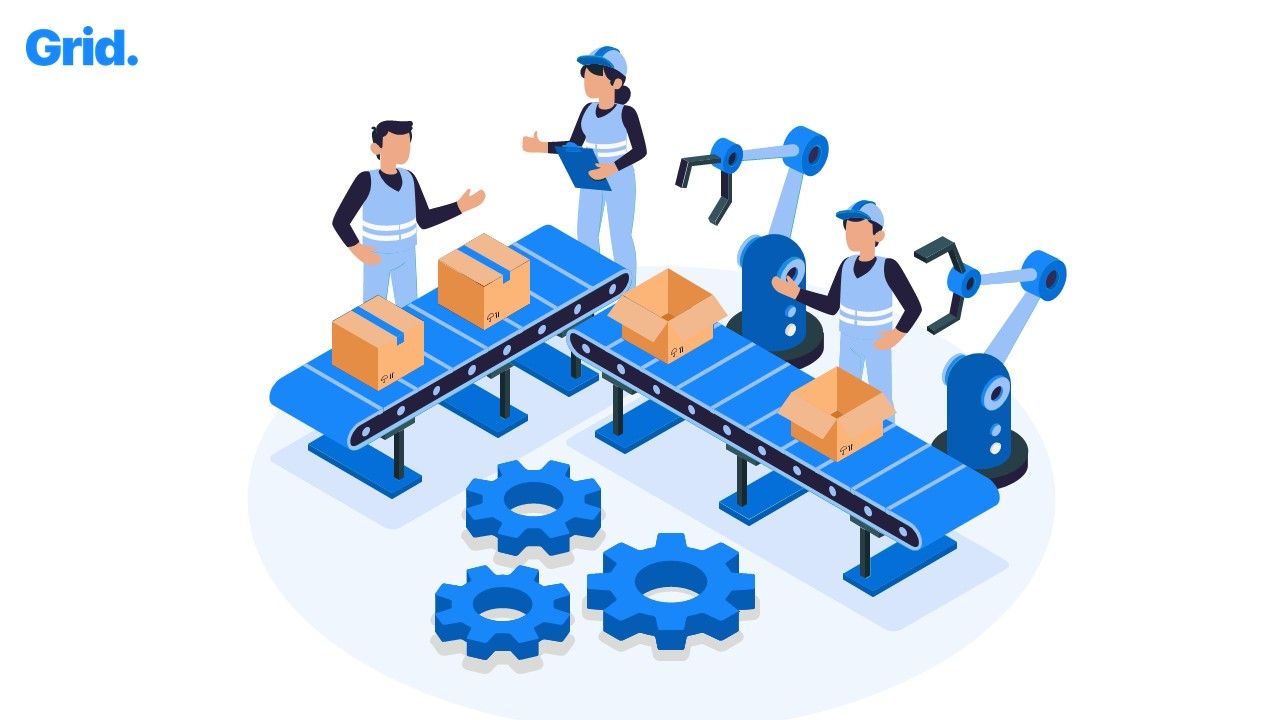
Productivity is critically influenced by proficiency in operations management, from factory line workers to decision-makers. Making sure every single personnel is productive as per requirements, and continuously working in line with business goals is essential. Manufacturing organizations need to have a holistic picture of their workforce's task completion rate because failure to do so results in human errors leading to the above four losses.
With Grid, organizations get access to comprehensive monitoring and managing workflows, with no-code applications tracking employee activity including leaves, breaks, and working hours along with detailed reports. Many a time, employees also fail to report minor issues owing to hesitance or ignorance, and this can sometimes develop into larger problems or habits. Having an application that collects data regularly without fail, makes sure you're managers and decision-makers have 100% visibility into even ground-level operations, thus nurturing an error-free environment.