Cybersecurity continues to be the most sought-after investment to fight against workplace disruptions, with companies extremely alert about the probability of cyber-attack-incurred losses. While organizations continue to invest all their time and money in securing their data, the lack of safety in the workplace keeps on amounting to cumulative losses that today outstrip the cost of any other form of disruption.
While a single incident might not amount to much and might seem like an event that comes with the occupation, the sheer frequency in a year significantly impacts workforce health and morale, compliance and regulations, equipment condition, and production downtime. A lack of initiatives in this space has got to do with how little visibility business owners get into the day-to-day operations with everything apart from a few select processes running manually or on traditional legacy systems. But of course, many industry leaders have successfully managed to eliminate health and safety losses and maintain a completely regulated workplace. So how do they ensure workplace safety round the clock?
Using Connected Worker Platforms, businesses can leverage digital technology and software to provide real-time data and insights on worker activities and environmental conditions. These platforms are operable through mobile devices and tablets, making it easier for frontline operations workers to continuously update data and communicate with other workers from anywhere. Being cloud-based, all the data that's being collected can be accessed in real time by site managers, who can monitor if everything is in place or not. But this is just a glimpse of what connected worker platforms are capable of, here are ten different ways in which they can turn your operations incident-free:
Real-time Monitoring
Connected worker platforms integrate with sensors and mobile devices to monitor worker activities and workplace conditions in real-time. This allows employers to detect potential hazards or risky behaviors before they lead to an accident. For example, supervisors can monitor the levels of toxic gases in the air to detect exposure risks or employee personal health inspections that alert the risk of a contagious disease spreading through the workplace.
Automated Alerts
When a critical event or danger is detected, connected worker platforms can send automated alerts to workers and supervisors. These alerts can be sent through mobile devices, wearables, or other communication channels. For example, if a worker falls or if a piece of machinery malfunctions, an alert can be immediately sent to supervisors and emergency responders. This allows for quick and effective responses to emergency situations.
Improved Communication
In heavy industries, it's essential for workers to be able to communicate with each other and with supervisors in real time. This helps to reduce the risk of miscommunication and ensures that workers can receive assistance quickly when they need it. For example, workers can use connected worker platforms to report hazards, request assistance, or receive guidance on safety procedures.
Training and Education
Connected worker platforms can be used to provide workers with training and education on safety procedures and best practices. This helps to reduce the risk of accidents caused by human error or lack of knowledge. For example, workers can use connected worker platforms to access online training modules or instructional videos on safety procedures. Employers can also use the data collected by these platforms to identify areas where additional training is needed.
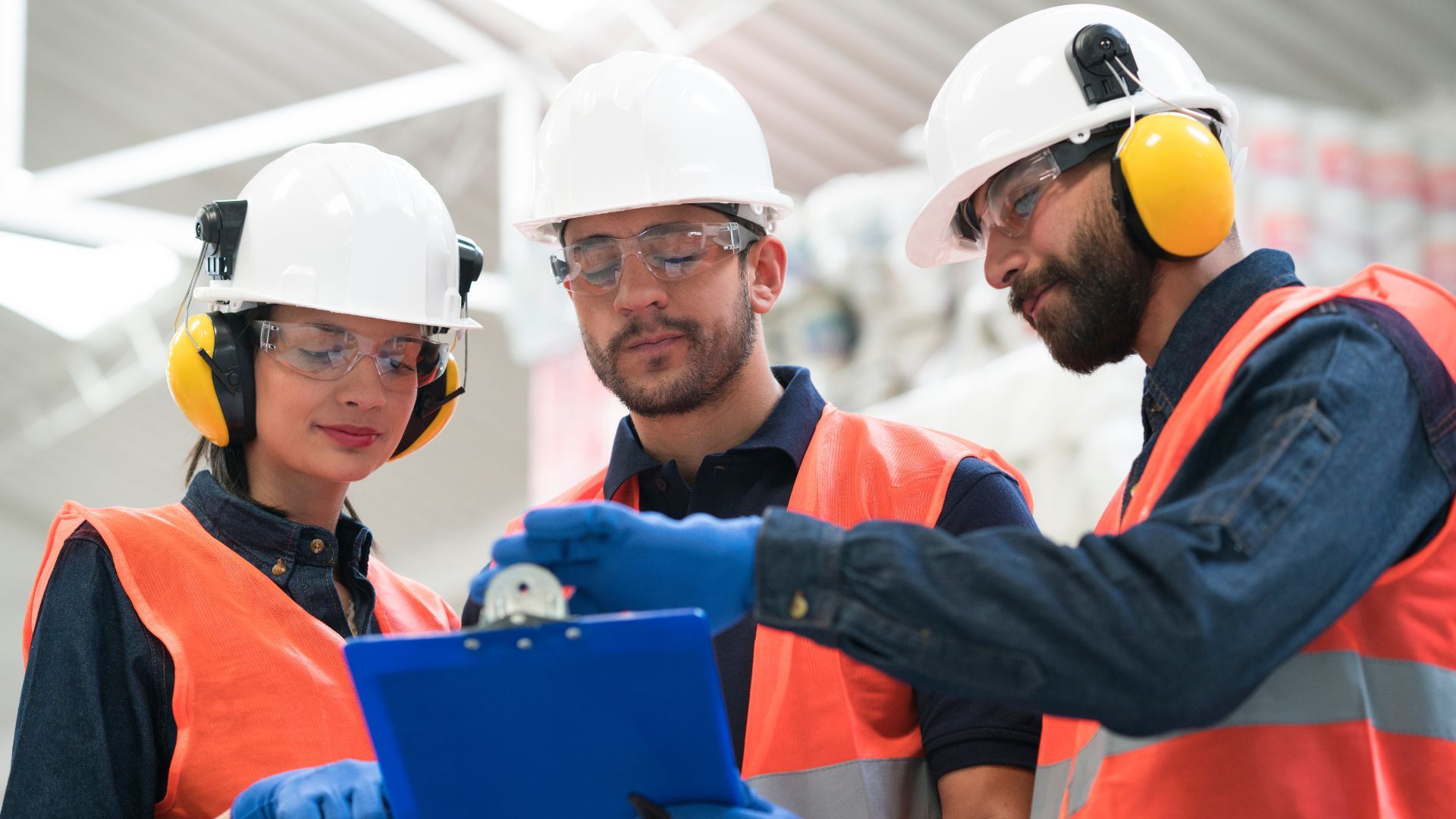
Data Analysis
For better safety planning or even to sustain the current condition, businesses need to collect data on worker activities and environmental conditions. This data can be analyzed to identify patterns and trends that can help employers to improve workplace safety over time. For example, employers can use the data to identify areas where workers are at high risk of accidents or to track the effectiveness of safety procedures. By continuously analyzing and improving upon this data, employers can create a safer workplace for their workers.
.jpeg)
Remote Supervision
Connected worker platforms can provide remote supervision of workers, which is especially useful in high-risk or remote environments. Remote supervision allows supervisors to monitor workers' activities and provide guidance or assistance as needed, even when they are not physically present. This helps to ensure that workers are following proper safety procedures and reduces the risk of accidents caused by miscommunication or lack of guidance.
Predictive Analytics
Connected worker platforms can use predictive analytics to identify potential safety risks before they occur. By analyzing historical data and identifying patterns and trends, these platforms can predict when and where accidents are most likely to occur. Employers can then take proactive measures to mitigate these risks, such as increasing safety training or adjusting work schedules to reduce fatigue.
Equipment Tracking
Connected worker platforms can track the location and condition of equipment, such as machinery or tools, in real time. This helps employers to ensure that equipment is being used properly and maintained appropriately, reducing the risk of accidents caused by faulty equipment or improper use.
Compliance monitoring
Connected worker platforms can monitor compliance with safety regulations and guidelines, ensuring that workers are following proper procedures and using appropriate protective equipment. This helps to reduce the risk of accidents and ensures that employers are in compliance with regulatory requirements, reducing the risk of legal or financial consequences.
Incident Reporting
Connected worker platforms can streamline the incident reporting process, making it easier and more efficient for workers to report accidents, near misses, or other safety hazards. By providing workers with a simple and accessible reporting mechanism, employers can quickly identify and address safety issues, preventing them from recurring and continuously improving their safety procedures. For example, a heavy industry like mining is prone to incidents and damages, and can highly benefit from applications that digitally record and generate reports instantly.