As industries evolve, manufacturers are constantly on the lookout for solutions that can streamline operations, improve efficiency, and enhance production quality. This is where Manufacturing Execution System (MES) software comes into play. MES software facilitates the tracking, management, and control of manufacturing processes on the factory floor, ensuring optimum utilization of resources and alignment with business objectives.
In 2023, there are a plethora of MES software available, but not all are created equal. After comprehensive research and analysis, here are the top 5 MES software solutions manufacturers should consider:
1. Plex Smart Manufacturing Platform
.jpeg)
Overview
Plex Systems provides a comprehensive suite of cloud-based manufacturing ERP (Enterprise Resource Planning) and MES (Manufacturing Execution Systems) solutions. The Plex Smart Manufacturing Platform is the core offering of Plex Systems, designed to help manufacturers streamline their operations, manage their shop floor, track inventory in real-time, and ensure quality control, among other functionalities. The platform is built on a modern, cloud-native architecture that allows it to scale easily and provide real-time data and insights to users across multiple locations and devices. Some of its key features include:
Key Features
1. Real-time Production Tracking
- Production Management: Instant visibility into production lines, enabling managers to identify bottlenecks and take corrective action promptly.
- Inventory Management: Provides insights into raw materials, WIP (work in progress), and finished goods, reducing carrying costs and ensuring optimum stock levels.
- Quality Management: Inbuilt tools for defect tracking, statistical process control, and other quality metrics ensure consistent product quality and compliance.
2. Financials and Analytics
- Financial Management: Track revenues, costs, and other financial metrics seamlessly integrated with the manufacturing data.
- Business Intelligence: Advanced analytics and reporting capabilities enable manufacturers to derive actionable insights, identify trends, and make data-driven decisions.
3. Integrated MES and ERP
- Unified System: Having MES (Manufacturing Execution System) and ERP (Enterprise Resource Planning) functionalities in one solution ensures seamless communication, reducing data discrepancies and errors.
- Supply Chain Management: Offers tools to manage suppliers, procurement, and shipment, streamlining the supply chain and reducing lead times.
4. Customization and Integration
- Tailored Solutions: The platform can be customized to suit specific industry needs and processes.
- Third-Party Integrations: Compatible with various other enterprise systems, enhancing its utility and ensuring comprehensive data collection.
5. Secure Cloud Infrastructure
- Data Protection: Offers robust security features including data encryption, regular backups, and secure access controls.
- Compliance: Ensures that data handling and storage comply with relevant regulations.
Industries
- Automotive
- Aerospace & Defense
- Food & Beverage
- Electronics
- Plastics & Rubber
- Metals
Why Choose Plex?
If you’re in search of a scalable MES solution that minimizes IT overhead and maximizes operational efficiency, Plex stands out as a strong contender.
2. Katana
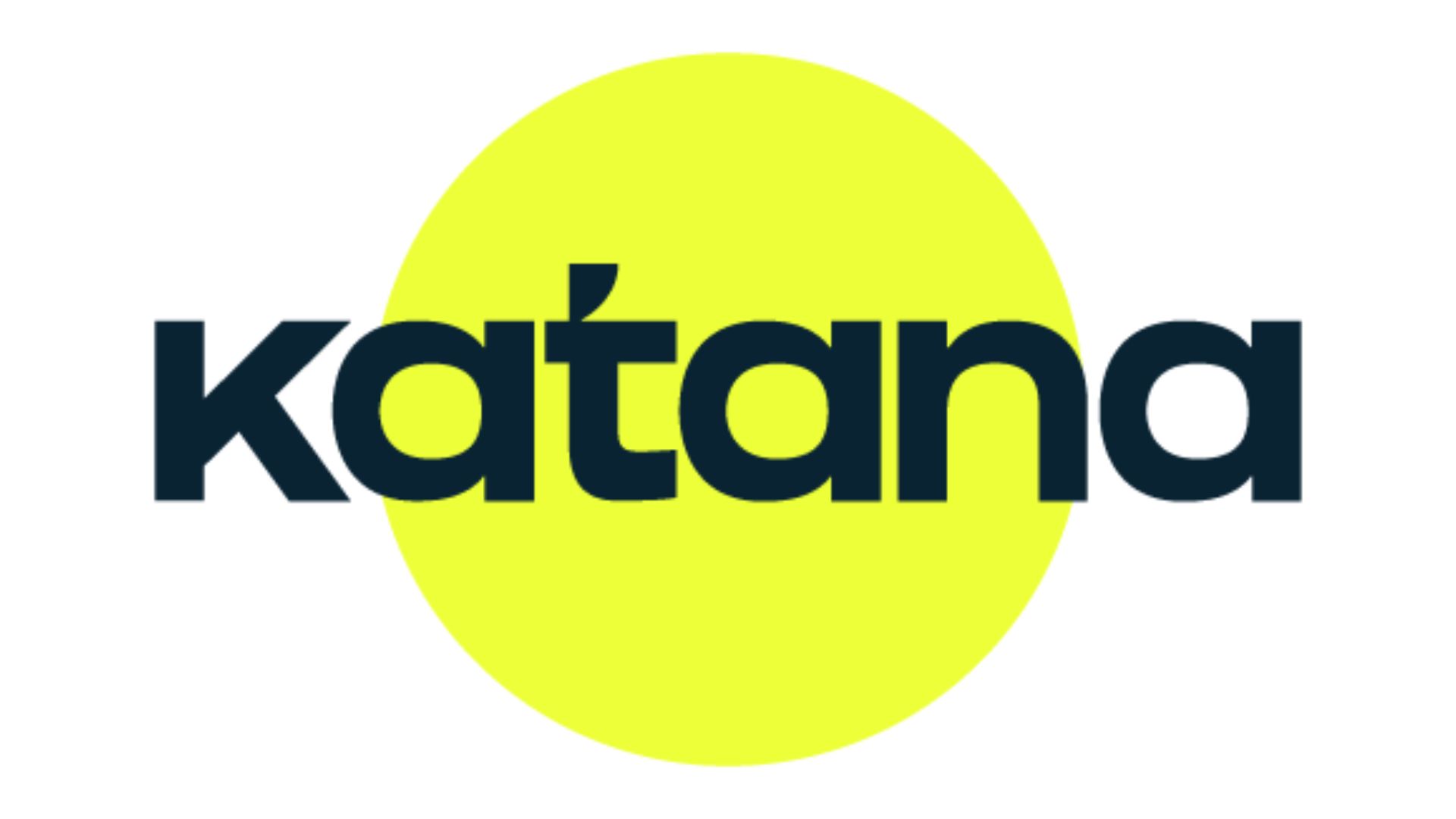
Overview
Katana is a cloud-based manufacturing software that helps small to medium-sized manufacturers manage their production processes, from a smart auto-booking system to ordering and scheduling to inventory management and shipping. The software is designed to be easy to use and customize, allowing manufacturers to tailor it to their specific needs and workflows. Best suited for SMEs, Katana simplifies complex manufacturing processes with its visually-driven interface and smart auto-booking system.
Key Features
1. Visual Production Planning
- Drag-and-Drop Interface: This helps manufacturers re-prioritize their orders and see the impact on their inventory in real-time. It offers a visual, intuitive way to manage production.
- Prioritization: Katana's auto-booking system prioritizes orders for you, meaning you can easily see which orders to fulfill first. This ensures that high-priority jobs get the resources they need.
2. Real-Time Inventory Control
- Automatic Inventory: Inventory is updated in real-time based on sales and purchases. You get an accurate overview of raw materials and finished goods.
- Floor-Level Control: Katana allows manufacturers to track their inventory at different stages of the production process.
3. Seamless Integrations
- E-commerce Platforms: Katana can be integrated with popular e-commerce platforms like Shopify, WooCommerce, and BigCommerce. This ensures real-time updates between sales and production.
- Accounting Tools: Integration with tools like QuickBooks or Xero means that financials are kept up-to-date automatically.
4. Multi-warehouse Support
- Warehouse Management: Manage stock across multiple locations, whether it's multiple warehouses, retail locations, or the production floor.
- Traceability: Track products with batch and serial numbers, which is crucial for quality control and recalls.
5. Sales and Purchase Modules
- Order Management: Easily manage sales orders, generate invoices, and keep track of your order fulfillment process.
- Supplier Management: Manage your suppliers, generate purchase orders, and ensure you never run out of the raw materials you need.
Industries
- Apparel and Footware
- Cosmetics
- Food & Beverage
- Electronics
- Furniture
- Industrial Manufacturing
- Automotive
Why Choose Katana?
Small to medium-sized businesses looking for an MES that seamlessly integrates with their sales platforms will find Katana to be a perfect match.
3. Tulip
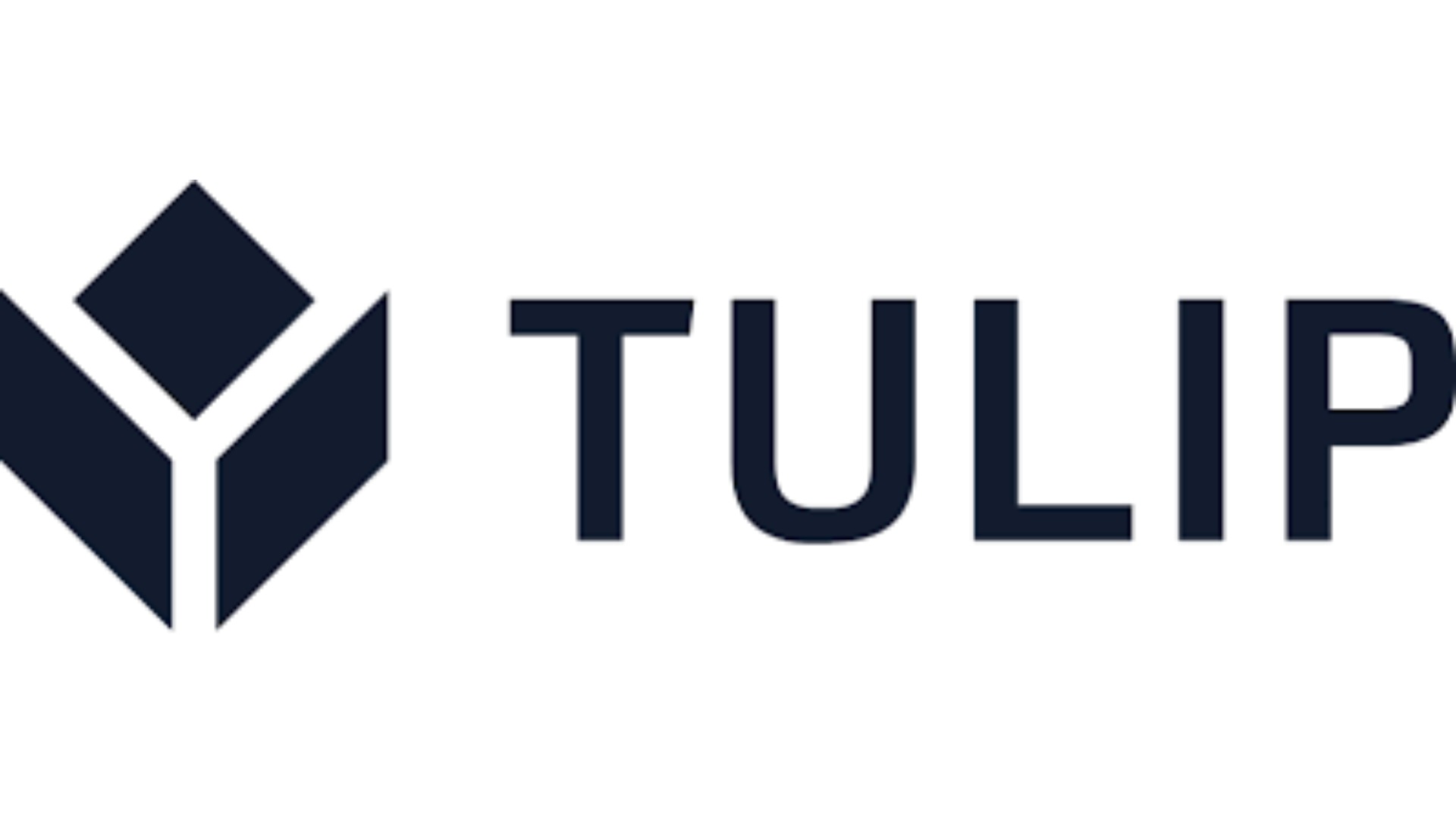
Overview
Tulip Interfaces, often referred to simply as "Tulip," offers a frontline operations management platform that allows manufacturers to develop applications to meet their specific needs on the shop floor. Going beyond traditional MES functionalities, Tulip's platform emphasizes the importance of human factors in manufacturing processes by providing tools that aim to augment the capabilities of frontline operations with modern technology. Here's a detailed breakdown of Tulip's features, functionalities, and benefits:
Key Features
1. No-Code Application Platform
- App Creation: Users can create shop-floor applications using a drag-and-drop interface without any coding knowledge.
- Templates: Tulip provides a variety of app templates to jump-start the creation process, catering to common manufacturing use-cases.
2. Shop Floor Analytics
- Data Collection: Capture data from manual operations, machines, and processes.
- Real-Time Insights: Interactive analytics dashboards offer insights into operations, helping manufacturers identify inefficiencies and areas of improvement.
3. Operator Feedback Loops
- Interactive Work Instructions: Create step-by-step interactive guides for operators, ensuring consistency and quality.
- Feedback Mechanism: Operators can provide feedback directly through the platform, leading to continuous process improvement.
4. IoT Integration
- IoT Gateway: Tulip’s platform integrates with a range of sensors, machines, and smart tools via their IoT gateway. This ensures real-time data collection from shop floor devices.
- Instant Feedback: Operators can receive immediate feedback from connected devices, helping in real-time decision-making.
5. Training and Workforce Development
- Training Modules: Create interactive training applications to onboard new employees or introduce new processes.
- Skills Tracking: Monitor and manage the skills and certifications of the workforce.
Industries
- Pharmaceuticals
- Medical Devices
- Automotive
- Electronics
- Aerospace & Defense
- Luxury Goods
- Consumer Products
Why Choose Tulip
For manufacturers that need a highly customizable MES solution without diving deep into software development, Tulip offers a perfect blend of flexibility and functionality.
4. Grid
.jpeg)
Overview
While Grid might be a newer name for some, it has carved a niche for itself by delivering powerful MES functionalities and integrating them with other enterprise systems.
Key Features
1. Process Control
- Workflow Management: Capabilities that enable manufacturers to define and automate production processes, including routing, scheduling, and quality checks. This helps ensure that production processes are consistent and repeatable, reducing errors and need for manual intervention.
- Production Planning: Empowers manufacturers to create and manage production plans, including scheduling, batch management, and material tracking. This helps ensure that production runs according to plan, with minimal delays or disruptions.
- Real-Time Monitoring: Manufacturers can optimize their production runs based on real-time data. This helps in immediate decision-making and reducing downtime.
2. Shop Floor Control
- Task Assignment: Grid provides features for assigning manufacturing tasks to team members and monitoring their progress.
- Shop Floor App: An additional mobile application for workers to update task statuses, ensuring real-time tracking.
3. Cloud-Native Solution
- Anywhere Access: Since it's cloud-based, manufacturers can access their data and the platform from anywhere, ensuring flexibility and real-time decision-making. The cloud architecture allows businesses to easily scale up or down based on their requirements.
- Operator Interface: Provides an intuitive operator interface that allows production staff to easily interact with the system. This includes visual dashboards, alerts, and notifications that provide real-time information about production status, equipment performance, and quality metrics.
4. Quality Management
- Inspection & Testing: Build quality inspection and testing apps that help in reducing defects and ensuring product consistency. This includes tracking quality metrics, managing defect rates, and implementing corrective actions as needed.
- Material Tracking: Allows manufacturers to track materials from receipt through production and shipping. This includes tracking material lots, serial numbers, and expiration dates, ensuring that materials are properly traced and accounted for.
Industries
- Mining and Mineral Exploration
- Electric Vehicles
- Industrial Manufacturing
- Apparel and Apparel Decoration
- SMART Infrastructure
- Construction
- Green Energy
- Hospitality
- Metals
Why Choose Grid
If you're a forward-thinking manufacturer who wants effortless digital transformation, Grid's emphasis on flexibility, integration, and analytics makes it a prime choice.
5. 42Q
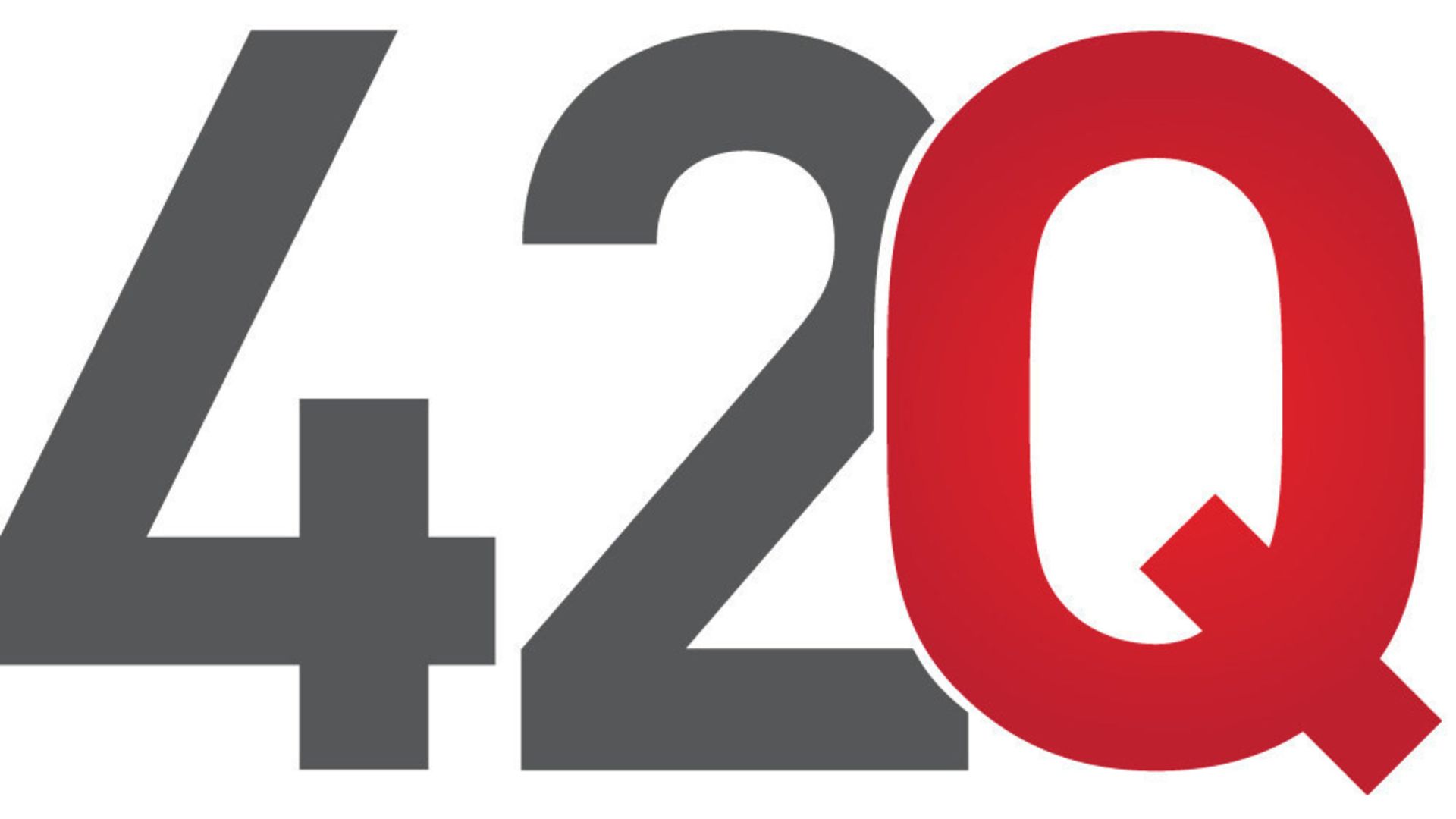
Overview
42Q’s cloud-native approach to MES ensures that manufacturers get robust functionalities without the constraints of infrastructure management. It's part of the Sanmina Corporation, a global electronics manufacturing services (EMS) provider. The MES solutions provided by 42Q are aimed at offering manufacturers greater visibility, control, and synchronization across their operations.
Key Features
1. End-to-end Visibility
- Dashboard: Provides real-time insights into operations, from machine status to inventory levels.
- Instant Notifications: Automatic alerts for any anomalies or issues, allowing for quick resolution.
2. Industry-specific Compliance Tools
- Standardized Processes: Ensures processes are consistent and meet industry standards.
- Electronic Records: Helps in maintaining electronic records, which is essential for industries that need to comply with regulations like FDA's 21 CFR Part 11.
3. Cloud-Based Solution
- Immediate Deployment: Being cloud-based, 42Q can be implemented quickly compared to traditional MES solutions.
- Scalability: Easily scalable to meet the needs of growing manufacturing operations.
- Reduced IT Overhead: With no need for on-premises servers or IT infrastructure, manufacturers can save on IT costs.
4. Machine Integration
- ERP Systems: Can be integrated with popular Enterprise Resource Planning (ERP) systems.
- IoT Devices: Integration with Internet of Things (IoT) devices ensures data from machines and sensors is fed into the system in real-time.
Industries
- Medical Devices
- Automotive
- Discrete Manufacturing
- Aerospace & Defense
Why Choose 42Q
If rapid deployment and scalability are your primary concerns, 42Q can deliver exceptional MES functionalities without the traditional constraints.
Conclusion
Choosing the right MES software is critical for any manufacturer looking to stay competitive in 2023. The above list highlights some of the best solutions available, each with its unique offerings. Evaluate your specific needs, scalability requirements, and integration preferences to make an informed decision. With the right MES, manufacturers can ensure smoother operations, improved productivity, and enhanced product quality.